Understanding Industry 4.0: The Fourth Industrial Revolution
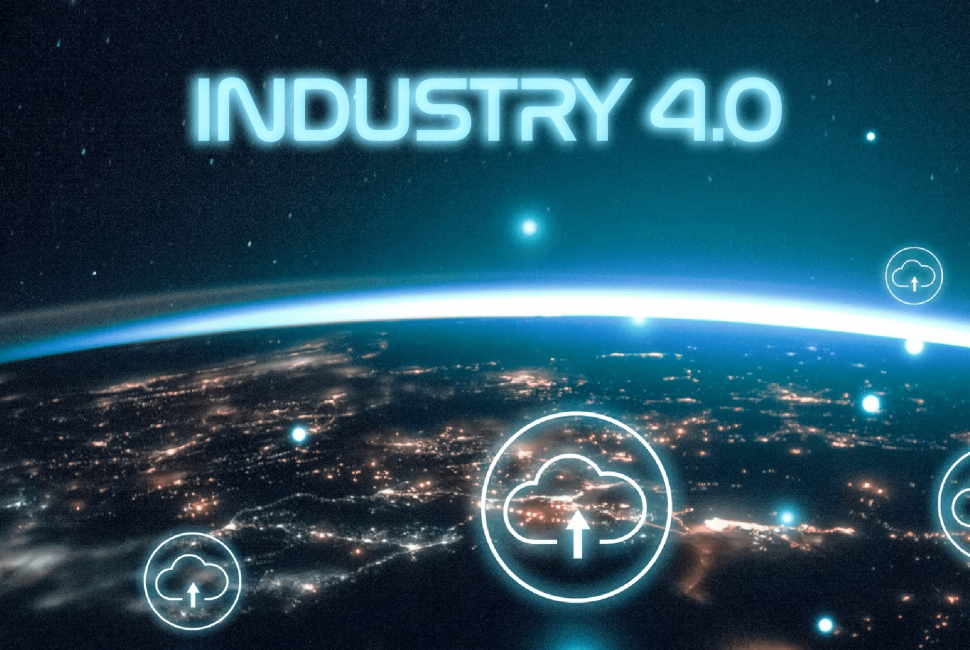
What is Industry 4.0?
Industry 4.0 is the term used to describe the application of digital technologies such as analytics, artificial intelligence, cloud computing, and the Internet of Things (IoT) to manufacturing, with the goal of connecting the entire production process and creating a smart factory. By leveraging these technologies, companies can create a more efficient, intelligent, and connected production system that can autonomously monitor, analyse, and optimise production processes.
The fourth industrial revolution is a new wave of advanced technologies and automation that is transforming many industries. Examples of Industry 4.0 include:
1. Autonomous robots: Autonomous robots, such as robotic arms and drones, are being used in manufacturing to automate processes and reduce human labour.
2. Artificial intelligence: AI-powered machines are being used to gather and analyse data, to control production processes, and to develop new products and services.
3. Big data: Companies are using big data to identify patterns in customer behaviour, optimise production, and create predictive models.
4. Internet of Things (IoT): IoT devices are being used to track and monitor production processes in real time, thereby increasing efficiency and accuracy.
5. Cloud computing: Cloud computing is being used to store and process data, to provide services over the internet, and to enable interconnectivity between devices.
What is Industry 4.0 certification?
Industry 4.0 certification is a type of certification that helps to ensure that businesses have the necessary tools and processes in place to implement Industry 4.0. It covers topics such as digital transformation, connected products, cyber-physical systems, big data and analytics, artificial intelligence, and the internet of things (IoT). This certification is becoming increasingly important as businesses strive to remain competitive in a rapidly changing technological environment.
What is the industry 4.0 concept?
Industry 4.0 is a concept of the fourth industrial revolution involving the integration of digital technologies into the manufacturing industry. It is characterised by the use of cyber-physical systems, such as the Internet of Things (IoT), robotics, cloud computing, big data, artificial intelligence (AI) and 3D printing. The idea behind Industry 4.0 is to enable machines to communicate with each other and to be self-organising, self-optimising and self-healing. Additionally, the concept encourages the development of more flexible and adaptive production processes that can be quickly changed to meet the needs of customers.
How will industry 4.0 change the future?
The Fourth Industrial Revolution, is ushering in a new era of automation through the use of technology such as the Internet of Things (IoT), Artificial Intelligence (AI), Robotics, 3D printing, and Cloud Computing. This means that many jobs that humans currently do will be replaced by automation. As a result, the future of work is expected to shift from manual labour to more analytical and creative roles. Additionally, as workers become more connected and empowered through technology, they will be able to work on more complex tasks, leading to an overall increase in productivity. Finally, Industry 4.0 is expected to create new jobs that are focused on managing and maintaining the technology that is being used. Overall, Industry 4.0 is set to revolutionise the future of work by making it more efficient, productive, and collaborative.
How will industry 4.0 affect society?
It will revolutionise the way people live and work, and it will change the way economies, governments, and businesses operate. Benefits will include improved productivity and efficiency, new jobs and opportunities, faster development of new products and services, and improved access to information. However, it will also bring disruption and inequality, as those who lack the skills to take advantage of the opportunities or access the new technologies may be left behind. Additionally, concerns about privacy and security, as well as the potential for displacement of workers, must be addressed.
Why is industry 4.0 important?
Industry 4.0 is important because it helps revolutionise the way products are made and services are provided. It is driving the transformation of traditional manufacturing and production processes into digitised, interconnected and automated processes. This transformation is enabling businesses to become more efficient, agile, and responsive to customer needs. It is also creating new opportunities for businesses to develop smarter, more personalised products and services that cater to customers’ individual needs. Finally, it is helping to reduce costs and increase profitability by decreasing waste and increasing production speed.
When and how did industry 4.0 start?
Industry 4.0 began in 2011 when the German government first introduced the concept in its High-Tech Strategy. It was developed as a response to the increasing number of connected devices and the need for more efficient coordination of the production process. Since then, the concept has been adopted by many other countries, companies, and organisations.
When will industry 4.0 reach the market?
Industry 4.0 is already in the market but it is still in its early stages. Companies are starting to invest in the technologies and processes associated with Industry 4.0, and are beginning to use them in their production processes. It is expected that Industry 4.0 will become more widely adopted over the next few years, as technologies and processes become more refined and cost effective.
Industry 4.0 in India
Industry 4.0 is the fourth industrial revolution, which is characterised by the integration of advanced technologies into the manufacturing process. Industry 4.0 is taking hold in India, where manufacturers are leveraging the latest advancements in automation, artificial intelligence (AI), machine learning (ML), robotics, and the Internet of Things (IoT) to enhance production and efficiency.
In India, Industry 4.0 is being implemented across various industries, including pharmaceuticals, automotive, textiles, and engineering. Companies are using Industry 4.0 solutions to reduce their operational costs, increase productivity, and improve the quality of their products.
The Indian government is also supporting the development of Industry 4.0, with the Ministry of Electronics and Information Technology (MeitY) launching the National Strategy on Artificial Intelligence in 2018. The strategy aims to promote the use of AI, ML, and IoT in various industries and to create an AI-ready workforce. The government is also making investments in research and development in Industry 4.0, as well as providing incentives for companies to adopt Industry 4.0 solutions.
Overall, Industry 4.0 is transforming the manufacturing landscape in India, helping manufacturers save time, money, and resources while creating high-quality products. Smart manufacturing in Industry 4.0 also has the potential to increase safety, security, and sustainability in the industry.
Advantages of Industry 4.0
1. Increased Productivity: Industry 4.0 is expected to increase the productivity of factories and production lines, as well as improve the quality and efficiency of their processes.
2. Advanced Automation: Automation is expected to become even more advanced with the implementation of Industry 4.0. Automated systems will be able to track and monitor performance and quickly adjust processes to improve efficiency.
3. Improved Quality: With Industry 4.0, manufacturers will be able to use data and analytics to identify potential quality issues and address them before they become problems.
4. Increased Visibility: With more advanced sensors, companies will have better visibility into their production processes. This will allow them to make more informed decisions and reduce waste.
5. Cost Savings: By reducing the need for manual labour and improving the efficiency of processes, companies can save money in the long run.
Disadvantages of Industry 4.0
1. Complexity: Implementing and maintaining an Industry 4.0 system can be complex and costly.
2. Cybersecurity Concerns: As with any system that relies on data, there are concerns over the security of the system.
3. Reliance on Tech: Companies could become overly reliant on technology, which can lead to inefficiencies and errors if the system is not properly maintained.
4. Job Losses: As automation becomes more advanced, there is a potential for job losses as companies reduce their need for manual labour.
5. Lack of Skilled Workers: Companies may find it difficult to find skilled workers to maintain and operate their Industry 4.0 systems.
Industry 4.0 Challenges:
1. Data security: The large amounts of data collected and stored by Industry 4.0 initiatives can make them vulnerable to cyber attacks and data breaches.
2. Technological complexity: Designing and deploying a successful Industry 4.0 initiative requires a deep understanding of the underlying technologies and a high level of technical expertise.
3. Cost: Implementing new technologies and processes can be expensive, and many businesses may not have the budget to do so.
4. Cultural resistance: Some employees may be resistant to change, as they may feel threatened by the introduction of new technologies.
5. Regulatory compliance: Businesses must take into account applicable laws and regulations when implementing Industry 4.0 initiatives.
Industry 4.0 Opportunities:
1. Increased efficiency: The automation of processes can result in improved efficiency and cost savings.
2. Improved customer service: The use of analytics and AI can enable businesses to better understand customer needs and provide more personalised services.
3. Enhanced decision-making: The use of big data and analytics can provide insights that enable businesses to make more informed decisions.
4. Increased collaboration: Industry 4.0 technologies can facilitate collaboration between different parts of the organisation and between organisations.
5. New business opportunities: Industry 4.0 technologies can enable organisations to develop new products and services.
Industry 4.0 and sustainability
Industry 4.0, also known as the fourth industrial revolution, is an emerging concept that focuses on automation and data exchange in the manufacturing industry. It has the potential to revolutionise the way that industries operate and, when thoughtfully addressed, can enhance sustainability.
The focus of Industry 4.0 is on intelligent, interconnected processes that leverage the Internet of Things (IoT) and other digital technologies to increase efficiency, reduce costs and improve customer satisfaction. For example, digital sensors are used to monitor the production process, allowing production managers to optimise resources and reduce waste. In addition, data-driven decision-making, enabled by big data analytics, can help manufacturers identify potential problems before they become costly issues.
When combined, these technologies can reduce the environmental impact of manufacturing. For example, intelligent automation can reduce energy use by optimising processes and eliminating waste. By connecting machines and systems, manufacturers can respond quickly to changes in demand, reducing the need for excess inventory. Additionally, predictive analytics can help identify potential problems before they lead to costly repairs or environmental damage.
By taking a holistic view of the industry and its environmental impact, Industry 4.0 can help manufacturers increase sustainability and reduce their carbon footprint. As the technology becomes more pervasive, it will be essential for manufacturers to develop strategies to ensure that sustainability remains a priority.
Conclusion
Industry 4.0 is an exciting concept that promises to revolutionise the manufacturing industry by leveraging the power of digital technology. By integrating automation, robotics, and the Internet of Things, factories can become more efficient and intelligent, leading to improved products and services. By leveraging new technologies such as cloud computing, augmented reality, and predictive analytics, manufacturers can gain a competitive edge in the market. Ultimately, Industry 4.0 has the potential to revolutionise the manufacturing industry and help companies remain competitive in a global market.